Blue skies.. nothing but blue skies smiling at me! Can you say I’m ready for summer? If there is one season I love above all, it is the season of warm temperatures, long day-light and short-sleeves flying! Sadly, the same season more often than not also means thunderstorms, accompanied by heavy rainfalls. I can remember more than one instance where I nearly lost control of my car due to heavy standing water on the road. But! – you say – it was only a small car. Surely a heavy vehicule such as an aircraft should not be affected by that problem. And yet, the crew and passengers of the Air France A340 Flight 358 that went off a runway at Toronto Pearson Int’l airport in August 2005 will testify otherwise.
(Read Part 1 of A landing you can walk away from – What to know about the most demanding phase of your flight – Runway Friction Index)
As you have probably deduced by now, hydroplaning does not only affect drivers. It is a day-to-day reality for pilots as well. It does not relate to the vehicule’s weight, but rather to it’s speed. So let’s take a deeper look into hydroplaning and try to understand this crucial factor that will most likely influence some of your decisions and challenge your skills during your flying career.
From January 1981 through January 1988, nearly 400 commercial airline traction-related accidents occurred. Aircraft ran off ends of runways or veered off shoulders. The resulting crew and passenger fatalities motivated intense research programs between government agencies and industry. [1]
WHAT IS TIRE HYDROPLANING? [1]
When aircraft tires or highway vehicle tires roll over watercovered or flooded pavements, water may penetrate between the tire and the pavement. This penetration results in the formation of water pressure which raises a portion of the tire off the pavement. This pressure increases as the speed of the vehicle increases, supporting more and more of the tire, until, at a critical speed termed the hydroplaning speed, the tire is supported only by the water and loses all contact with the pavement.
It is obvious that many dynamic elements are involved in hydroplaning. To help understand these elements better, here is a more scientific definition of the phenomenon:
The force on the tire can be resolved into its vertical and horizontal components, commonly called lift and drag, respectively. When the lift force equals the weight force transmitted to the wheel, hydroplaning will occur. The amount the tire lifts off the pavement surface depends on the tire shape, water depth, and the speed of the vehicle. There will obviously be an equilibrium position of the tire for each speed greater than that required for incipient (starting, start of) hydroplaning. [2]
Admittedly the tire-hydroplaning phenomenon is quite complicated. Perhaps at one stage the hydrodynamic aspects o f the phenomenon are dominated by viscous effects (Viscous Hydroplaning), at another by inertia effects (Dynamic Hydroplaning) and at a later stage by thermodynamic effects, or reversion of the rubber and formation of steam pocket (Reverted Rubber Hydroplaning). At each and every stage, of course, the elastic properties of tires and their texture and geometry, as well as the relative roughness o f the wet pavement (Grooving), enter into the problem. For those cases of hydroplaning where velocity is quite high and the water is relatively deep, it seems rather reasonable to assume that the viscosity effects become insignificant. [3]
Wow, that was a lot of big words! I hope your head isn’t buzzing like mine! Just in case, let’s summerize this information into easier concepts.
Hydroplaning factors are mainly
1) Water Depth
2) Velocity of vehicule
3) Tire shape and thread
The three main types of hydroplaning, in increasing order of velocity, are
1) Dynamic Hydroplanning: Due to standing water on the runway that is at least one-tenth inch deep where the tire is completely supported by water. As the speed of the airplane and the depth of the water increase, the water layer builds up an increasing resistance to displacement, resulting in the formation of a wedge of water beneath the tire. When the water pressure equals the weight of the airplane, the tire is lifted off the runway surface and stops rotating. Directional control and braking is lost.[5]
2)Viscous hydroplaning is due to the viscous properties of water. A thin film of fluid no more than one thousandth of an inch in depth is all that is needed. The tire cannot penetrate the fluid and the tire rolls on top of the film. This can occur at a much lower speed than dynamic hydroplane, but requires a smooth or smooth acting surface such as asphalt or a touchdown area coated with the accumulated rubber of past landings. Such a surface can have the same friction coefficient as wet ice. And although this kind of hydroplaning may seem as ‘vicious’ as a mad dog when you encounter it, please remember it is pronounced like “vis-kus”.[5]
3) Reverted Rubber Hydroplaning: Occurs where a hot tire boils water on a wet runway surface after a long skid – the steam prevents the tire from contacting the runway. Reverted rubber hydroplaning frequently follows dynamic hydroplaning, during which time the pilot may have the brakes locked in an attempt to slow the airplane. Eventually the airplane slows enough to where the tires make contact with the runway surface and the airplane begins to skid. Reverted rubber hydroplaning is insidious in that the pilot may not know when it begins, and it can persist to very slow groundspeeds (20 knots or less) [5]
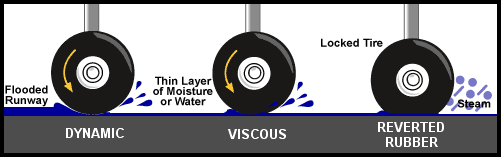
Source: FAA
HOW TO CALCULATE HYDROPLANING
Countless formulas can be found concerning hydroplaning. The fact of the matter is that, the dynamics of hydroplaning change constantly and from scenario to scenario, as we could understand from the definition. NASA hosts a quantity of information and PDFs describing the extensive research that it conducted on hydroplaning, and all the relevent formulas can be found with little work.
However, I am no physicist and a complicated string of equations is the last thing to go through my mind as I am planning and briefing an approach. So here are the only two formulas you will ever need to know as a pilot:
Hydroplaning speeds (KTS) = Vp
Rotating tires (Dynamic, Reverted Rubber Hydroplaning): 9.0 X √Tire Pressure (PSI)
Non-Rotating tires (Viscous Hydroplaning): 7.7 X √Tire Pressure (PSI)
Example: PC12NG landing after a thunderstorm just went through the area, deep amounts of water expected on ungrooved runway. Expecting dynamic hydroplaning. Tire pressures on main landing gear: 60 PSI. Hydroplaning speed: 9.0 X √60 = 70 KTS
Since the Vref of a PC12 at a normal flaps setting of 15° is 101 KTS, you should expect and brief a chance of hydroplanning upon landing until deceleration to under 70 KTS, especially if any crosswind component is expected.
Now we understand hydroplaning, and we learned how to prepare for it. But what can we expect from it? Let’s quickly review the main concequences of hydroplaning and the reasons why we need to be knowledgable about it.
WHAT ARE THE CONSEQUENCES OF TIRE HYDROPLANING? [1]
- Longer vehicle and/or aircraft stopping distances required
- Potential loss of directional control
- Greater sensitivity to crosswinds
- Greater reliance on reverse thrust for stopping
With that information in mind, be sure to brief your landing accordingly next time you expect higher-than-normal volumes of water on the runway. Especially during crosswind operations, on an airplane devoid of reverse thrust, or using shorter runway than usual, hydroplaning can be a very potent hazard.
Many resources are available to pilots to allow them to make good decision making and planning when facing hydroplaning.
The proper technique will go a long way in avoiding or decreasing the effects of hydroplaning:
1) It is best to land on a grooved runway if available.
2) Touchdown speed should be as slow as safely possible.
3) After the nosewheel is lowered to the runway, moderate braking should be applied.
4) If hydroplaning is suspected, the nose should be raised and aerodynamic drag used to decelerate to a point where the brakes do become effective.
5) Proper braking technique is essential. The brakes should be applied firmly until reaching a point just short of a skid. At the first sign of a skid, the pilot should release brake pressure and allow the wheels to spin up.
6) Directional control should be maintained as far as possible with the rudder.
RFI (see Part 1 of this series) might be available if the viscosity of the runway has degraded. Although it is usually more related to winter operations, make sure to obtain the information if it is available via NOTAMs or ATIS.
With the past and current research from NASA and other agencies, many improvements have been made to runway surfaces. Some airport now offer grooved runways, allowing for a near-dry friction coefficient even during rain-fall. Grooved pavement provides escape routes for water compressed between tire tread and pavement, and consequently, enhances braking and corneringAs expected, grooved runway surfaces have significantly greater friction properties than nongrooved surfaces, particularly at the higher speeds. [1]
Finally, improved tire designs have come a long way to promoting better traction during landing. The grooves of rubber tires are specially designed to ensure proper dispersal of water from under the tire, producing friction even during operation in a wet environment. The design and depth of tread, vehicle weight, tire pressure, and the water depth all influence hydroplaning. The thinner and longer the contact area, the less is the probability of hydroplaning. Wide and lightly loaded tires present the maximum risk. Deep tread disperses water more easily. Under inflated tires are more vulnerable to hydroplaning, particularly when the vehicle weight is more. Vehicles with trailers may be exposed to irregular hydroplaning due to the irregular weight distribution. An empty trailer will hydroplane sooner than the prime mover. Directional tread tire design, also known as unidirectional, are normally used for increased hydroplaning resistance. The numerous tread grooves are shaped to intensify the tire capability for channeling of water between the road and the tire. [4]
********************************************
In the next instalment of this series, we will take a look at crosswind landing factors and techniques. Stay tuned!!!
Read Part 1 of A landing you can walk away from – What to know about the most demanding phase of your flight – Runway Friction Index
[…] This post was mentioned on Twitter by Jean Denis Marcellin, Jean Denis Marcellin. Jean Denis Marcellin said: A landing you can walk away from – What to know about the most demanding phase of your flight (Part 2) http://wp.me/pC0AO-3E […]
[…] Part 1 of A landing you can walk away from – Runway Friction Index) (Read Part 2 of A landing you can walk away from – Runway Friction Index) The fact remains, though, that crosswind landings will always be part of […]
[…] formula tire pressure dynamic hydroplaning jdmarcellin.wordpress.com […]